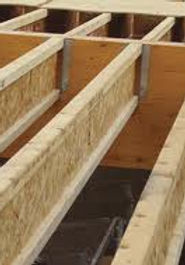
Engineered timber joists spanning onto Glulam beam
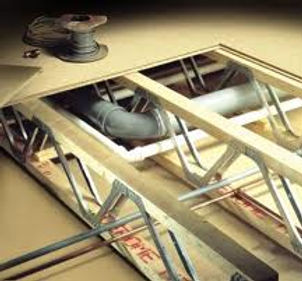
Metal web joists with service voids
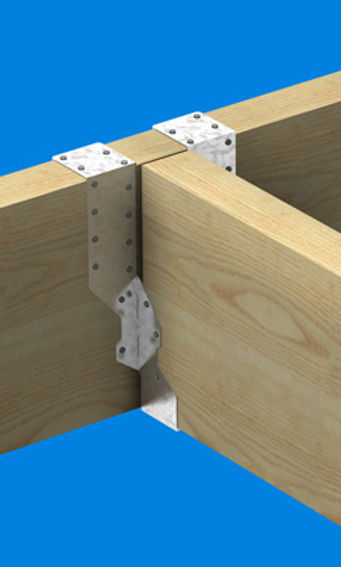
Joist hangers are required on unsupported connections
Floors
Moving up...
When we refer to floors in this instance, we are talking about the separating floor between levels. For ground floor level see foundations. At ground floor it is fairly common for older houses to use timber joists and floorboards. However, modern building regulations require higher levels of insulation at ground floor level. For this reason many builders will use either solid concrete or beam and block systems. These allow a continuous layer of insulation to be installed across the entire ground floor.
Traditional first floor joists are typically made from solid softwood timber. Depending on the span required these vary in depth from 89-300mm and in width from 50-100mm. It is impossible to give an ‘average’ size simply because it depends on the span and the loads the joist must support. For this reason, floors will have a fixed depth and either multiple joists or wider joists will be used in specific areas as required. For example, around a stairwell opening it is common to have a double or triple joist to ‘trim out’ the required void. Solid timbers cannot accommodate large service holes and can be prone to shrinking and twisting over time.
A more modern alternative are engineered timber joists. These comprise two softwood flanges and a central web made from engineered board such as OSB (oriented strand board). They are free from material defects so strength can be predicted with a greater degree of accuracy. They can span further than solid joists for a given depth and they are lighter than solid joists so can be easily transported on site. Large service holes can be cut through the central web and some even come with pre-punched ‘knockout’ holes. They have greatly reduced moisture shrinkage and are far less
Engineered floor solutions often require solid timbers in high strength areas. It is not recommended to use engineered products with traditional timbers because the moisture contents difference between the two can lead to shrinkage over time. Instead, a range of engineered beams can be used. These are Glulam, Kerto and Parallam to name a few. Engineered beams are manufactured by laminating thin strips of stress graded timber together to create a beam with very few defects – all knots etc can be removed to create a beam with less weak spots. For this reason they are stronger than solid timber joists and so can span further and be used to support greater loads.
Metal web joists are a further extension of engineered joists. These allow large diameter services (such as heat recovery system ducting) to pass anywhere along the joist but, in a similar way to trussed rafters, must be designed using specialist software so lead times must be increased. Also, site flexibility is reduced should any alterations be required.
Nobody wants a flexy floor so it’s important that building designers surpass the minimum design requirements for floors. At Delta Timber Frame we are always sure to add strength to intermediate floors where required to achieve a robust, quality feel.
All of our floors are constructed off site where possible. This has several benefits for your build programme. Joisting out a floor takes a long time but is usually quite straightforward. Main supporting beams are installed first – say around stairwells etc, and infill joists are added to fill in the gaps. Any unsupported beam ends have joist hangers attached and decking must be added over the joists. With our system, the majority of the structural beams along with the infill joists and any required hangers are formed into a series of ‘cassettes’ which can be manufactured, delivered and craned into position in one piece (essentially a large jigsaw puzzle!). This minimises site labour time, guarantees no delays through bad weather, benefits from factory tolerances and allows decking to be pre-installed giving an instant working platform to continue working from. For a standard house (250m2), our floors are normally completed within a single day. An added benefit is that the site is made safer since there is less chance of site workmen accidentally falling through gaps between joists during the construction phase.
Where flat roofs and occasionally pitched roofs will allow, we always aim to utilise our flooring system to reduce site labour and decrease build programmes.
